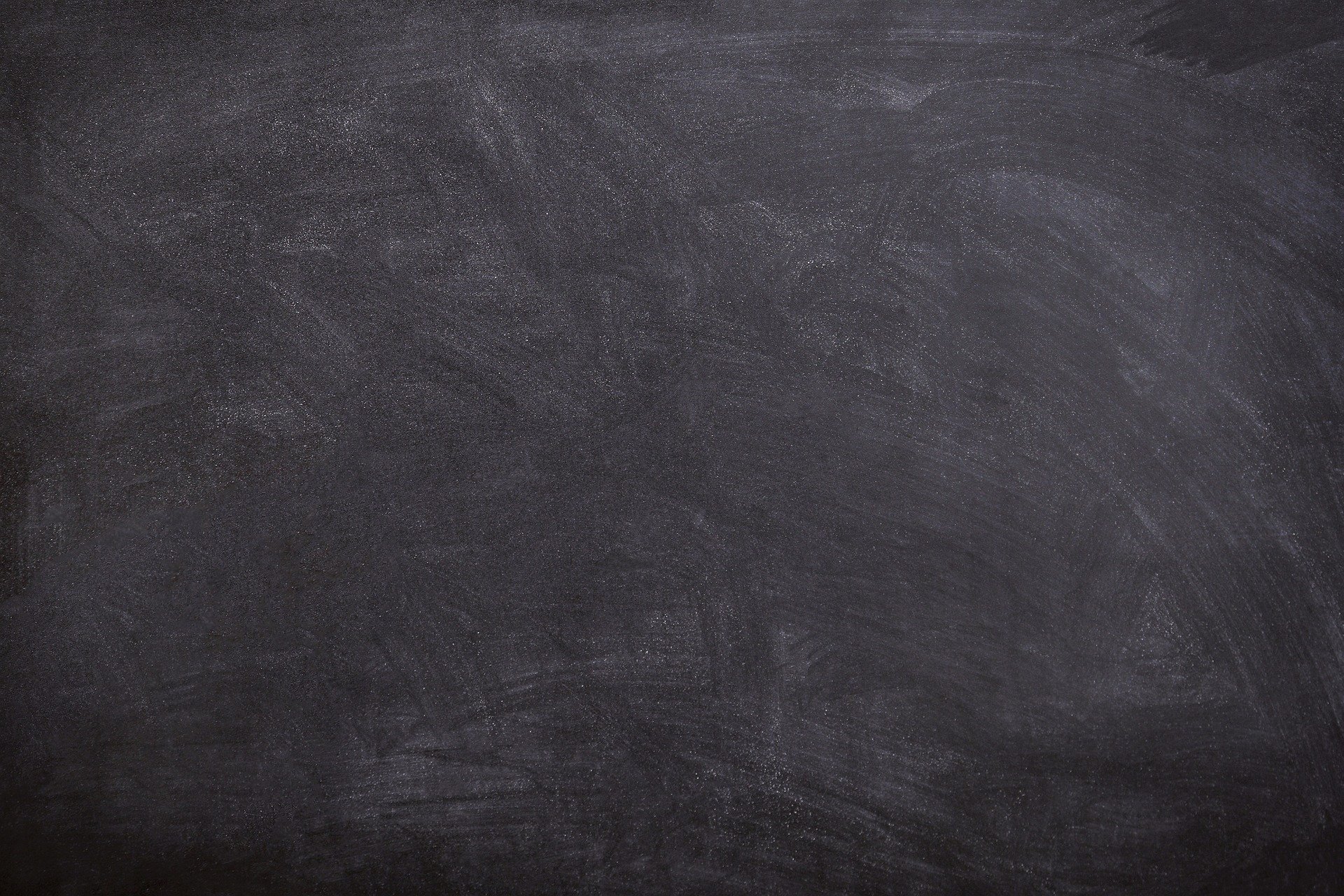
The history of lean thinking
Lean is a business management philosophy that originated in the manufacturing industry in the early 20th century. It was developed by a man named Taiichi Ohno, who was an engineer at Toyota. Ohno observed that there was a lot of waste in the manufacturing process and set out to find a way to eliminate it. He called this approach the "Toyota Production System" (TPS).
The TPS was based on two main principles: "Just-in-Time" (JIT) and "Jidoka." JIT is a method of production in which materials and components are delivered to the factory just in time to be used, rather than being stockpiled in advance. This helps to eliminate waste by reducing the amount of inventory that needs to be stored. Jidoka is a system of quality control in which machines are designed to stop automatically if they detect a problem, rather than continuing to produce defective parts. This helps to identify and correct problems quickly, before they can cause delays or defects in the final product.
In the 1980s, American manufacturers began to take notice of the success of Toyota and the TPS, and started to adopt elements of the system for themselves. They called this new approach "Lean Manufacturing." The term "Lean" was chosen to highlight the focus on eliminating waste and reducing inventory, which is one of the key goals of the TPS.
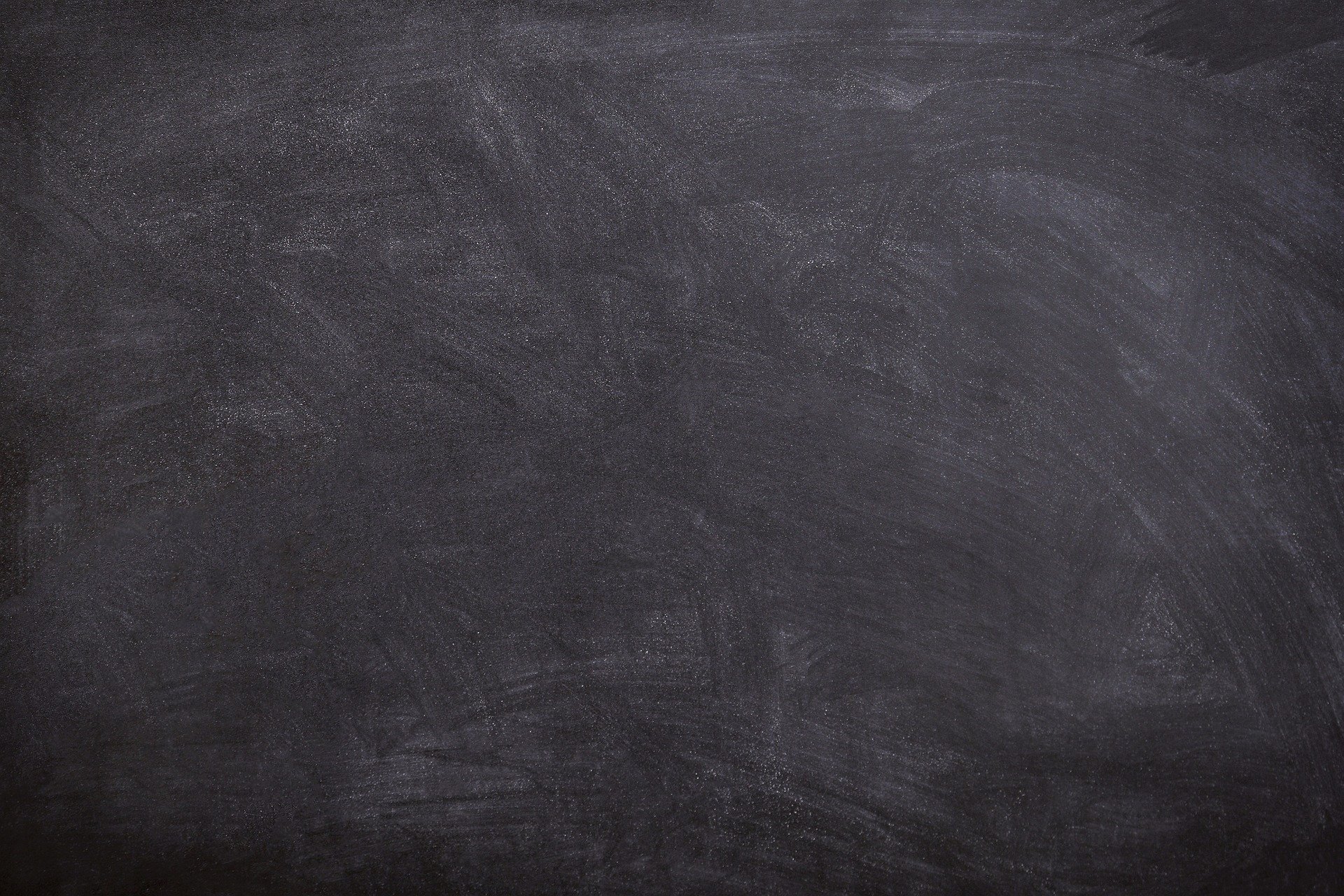
LEAN
MANUFACTURING
Lean Manufacturing is based on the same principles as the TPS, but it has been adapted to fit the needs of different industries and companies. The key elements of Lean Manufacturing include:
flow
value
perfection
pull
Value: Identifying and focusing on the activities that add value to the customer, and eliminating or reducing those that do not.
Flow: Ensuring that products and services flow smoothly through the value stream, without delays or interruptions.
Pull: Using customer demand to pull products and services through the value stream, rather than pushing them through based on production schedules.
Perfection: Continuously improving the value stream in order to achieve perfection, or the state of having no waste.
In the 1990s, a book called "The Machine That Changed the World" was published which popularised the term Lean production and helped to spread the word about the success of the TPS. The book was based on a study of the TPS by a group of researchers from MIT, and it highlighted the many benefits of Lean Manufacturing, including higher quality, lower costs, and faster delivery.
In recent years, there has been a growing interest in applying Lean principles to the public sector, such as government and non-profit organisations. This approach is often called "Lean Government" or "Lean Six Sigma." It involves using the tools and methods of Lean Manufacturing to improve efficiency, reduce waste, and increase value in the public sector.
With such successful provenance in industry and business, embracing lean principles in everyday life processes outside of work can lead to a more balanced, enjoyable, and efficient lifestyle. By applying these concepts to various aspects of life, we can simplify routines, reduce stress, and create more time for the activities and people that truly matter. Lean helps us prioritise what brings value and happiness, fostering a mindful and intentional approach to living that enriches our overall well-being and personal growth.